UPDATE: Fire and Sound Manual Released
New Fire and Sound Manual released to increase ease of access by architects.
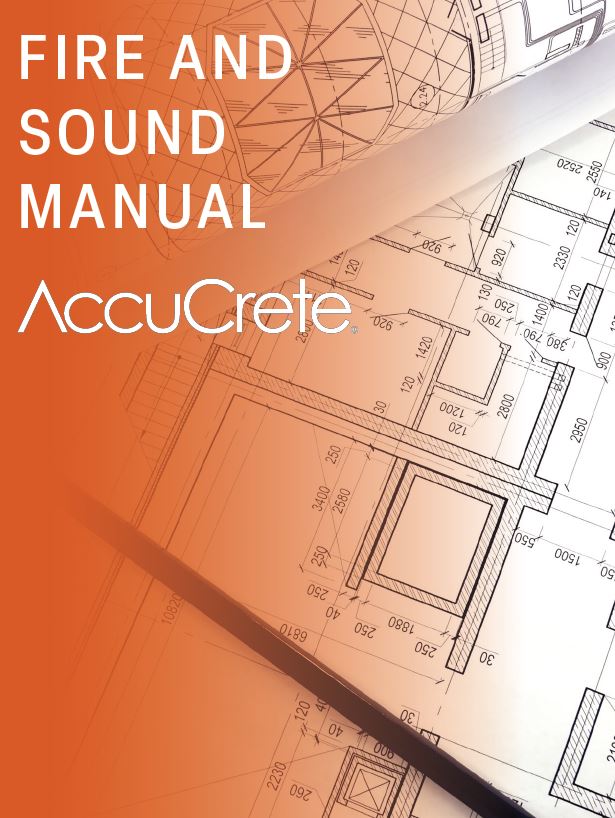
The Fire and Sound Manual
When designing UL assemblies, it’s important to maintain a balance between acoustic isolation and fire protection. Both are essential for safety and comfort. Our designs all conform to the limits specified in the UL Design. This includes variables like insulation thickness, where and how it’s placed in the cavity, and resilient channel spacing, and much more.
Image samples:
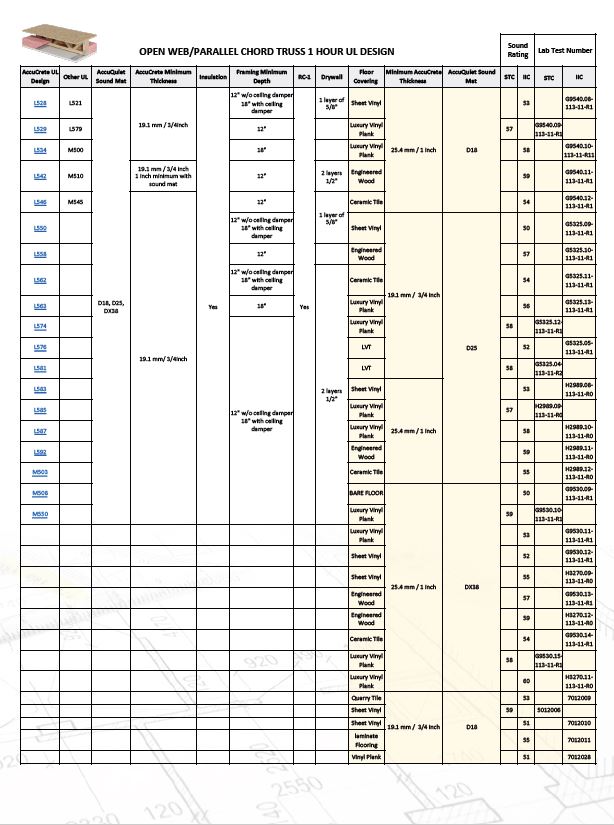
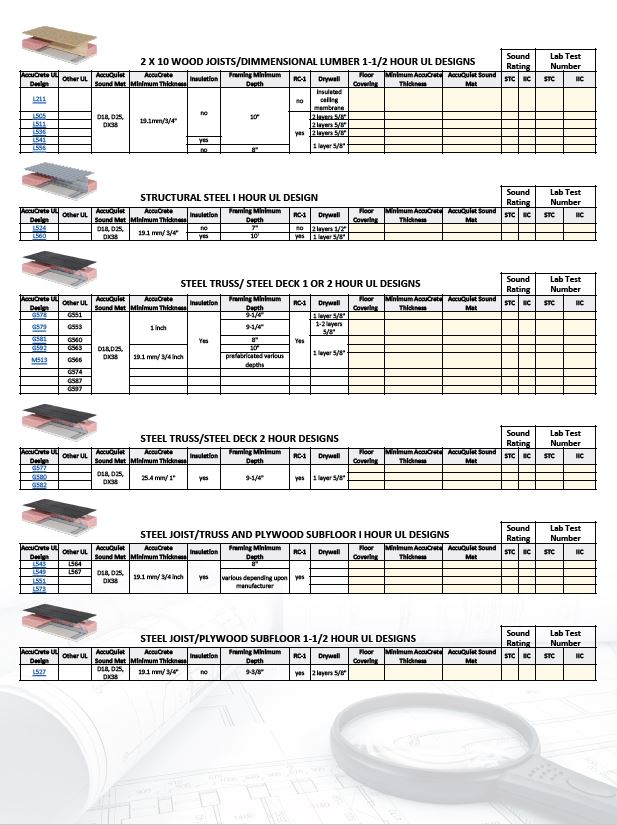
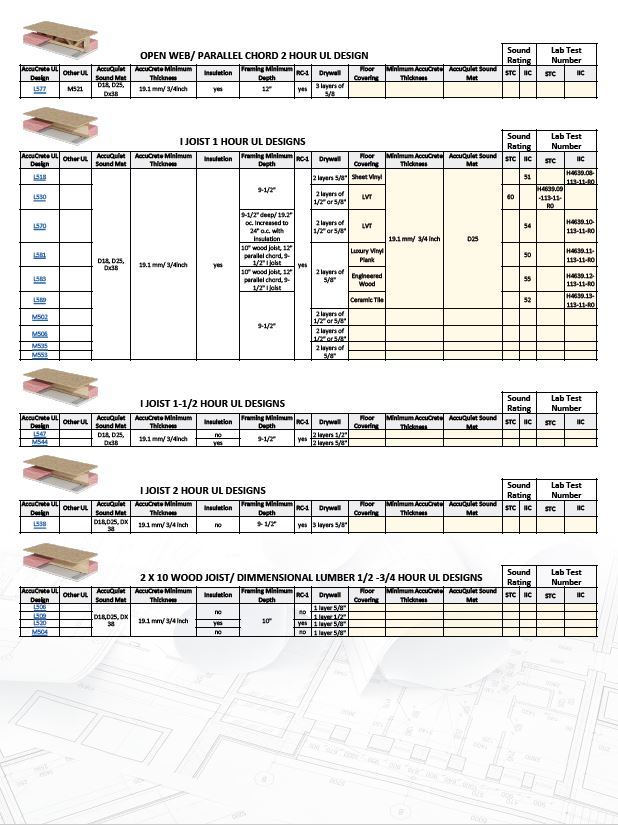
Content excerpt from the Fire and Sound Manual:
AccuCrete® and AccuLevel® underlayments are manufactured to rigorous ASTM standards, and have been tested to meet UL 1 and 2 hour fire rated designs. All AccuCrete® and AccuLevel® UL designs incorporate ultra low compressive AccuQuiet Sound Mats.
- Section 1207.1 of the 2018 I. B. C. scope applies to common interior walls, partitions and floor/ceiling assemblies between adjacent dwelling units or between dwelling units and public areas.
- Section 1201.2 of the 2018 I. B. C. scope applies to airborne sound for walls, partitions and floor/ceiling assemblies must have a sound transmission class (STC) of minimum 50 when tested in accordance with ASTM E90, laboratory test. Minimum 45 if field tested.
- Section 1207.3 of the 2018 I. B. C. scope applies to structure borne sound refers to floor/ceiling assembles between dwelling units or dwelling units and a public area must have an impact insulation class (IIC) of minimum 50 when tested in accordance with ASTM E492, laboratory test. Minimum 45 if field tested.
To download the Fire and Safety Manual – Click Here
More Apartments Needed in US
New apartment units needed to mitigate issues related to apartment demand and the shrinking supply of affordably priced housing.
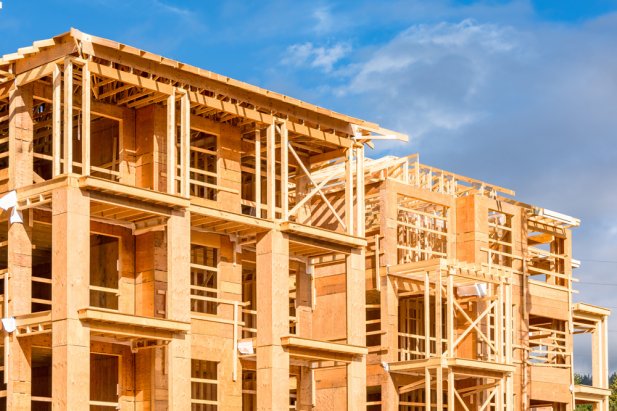
The U.S. needs 4.3 million new apartment units between now and 2035 in order to mitigate issues related to apartment demand and the shrinking supply of affordably priced housing, according to research commissioned by the National Multifamily Housing Council and National Apartment Association.
This number incorporates an existing deficit of 600,000 apartment homes, which the study attributes to underbuilding associated with the 2008 economic downturn. In addition, between 2015 and 2020, the nation’s supply of affordable housing — defined as housing units with rents less than $1,000 per month — declined by 4.7 million units.
Caitlin Sugrue Walter, vice president of research for the NMHC says “The main reason for these units not existing is that we have had a reverse filtering phenomenon occur because of our supply shortage. Because there are not enough available units, it moves the asking rents up, reducing the number of affordable units.”

Currently, the U.S. has a population of 36.8 million apartment residents living in 21.3 million apartment homes. Approximately 266,000 new units need to be built each year to meet the demand for more, according to the report.
The full study estimates apartment demand from 2022 through 2035 at the national, state and top 50 metro level. Variables in this estimate include the homeownership rate — projected to increase by 3.8% — and immigration. While the immigration rate stands at a record low, a reversal of this trend could significantly raise apartment demand, according to a press release on the report.
The site also offers a calculator to estimate the economic contributions and impact of building in a given area, with variables based on building size and type.
Making progress
At the state level, Texas, Florida and California account for 40% of future demand. The report estimates that these three states together will require 1.5 million new apartments by 2023.
Walter noted that many jurisdictions in Texas are performing well toward the apartment construction estimates outlined in the report.
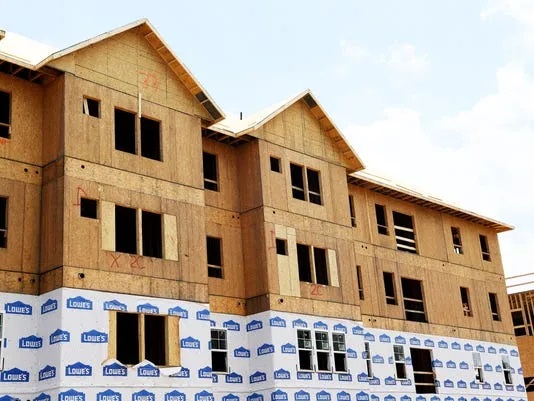
“[This] is good, because they comprise the bulk of the demand going forward,” Walter said. “[The] Dallas metro area has been leading for quite some time in terms of the number of projects being built.”
The report outlines a number of policy recommendations that the NMHC and NAA say will help solve the issues it presents. They include:
- Policies at the local level that support housing construction, such as by-right housing development and reduced parking requirements.
- The expansion of public-private partnerships.
- The enactment of state laws that override local restrictions.
- Federal policy in support of new construction, particularly affordable housing.
- “There are some things that can be done at the federal level, such as creating incentives for localities to examine their local policies,” Walter added. “Regulations are a huge driver of construction costs, which makes it difficult to build at lower, more affordable price points.”
This article appeared on the website “Multifamily Dive” and can be read in its entirety here: https://www.multifamilydive.com/news/to-meet-demand-us-needs-43m-more-apartments-by-2035/628358/
PROJECT PROFILE – Twin Hills Country Club, Oklahoma City, OK
This renovation of an iconic country club put AccuLevel® G-40 to the test.
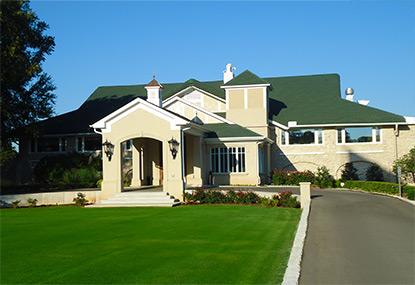
PROJECT OVERVIEW
Twin Hills Country Club had a real problem. Fortunately, AccuLevel® G-40 was the perfect solution. The golf course in Oklahoma City, OK was in the middle of a major renovation and addition to their iconic clubhouse.
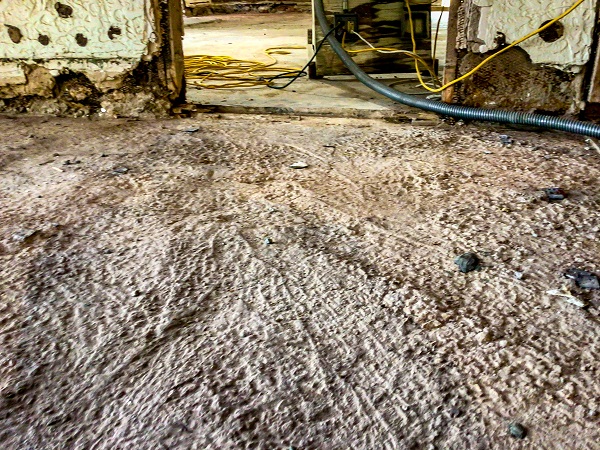
PROJECT DETAILS
The history of Twin Hills dates back to 1920 and has hosted several prestigious tournaments over the years including the PGA Championship, with players including Johnny Revolta, Arnold Palmer, and Gene Sarazen.
After removing the existing floor, they facing a huge challenge with the subfloor. The previous design used cinder block slabs, a common practice 80 years ago, but it left a big problem. How do you get a level floor when that subfloor looks like a gravel road. And just capping it with concrete was not a solution due to needing to remove the supports.
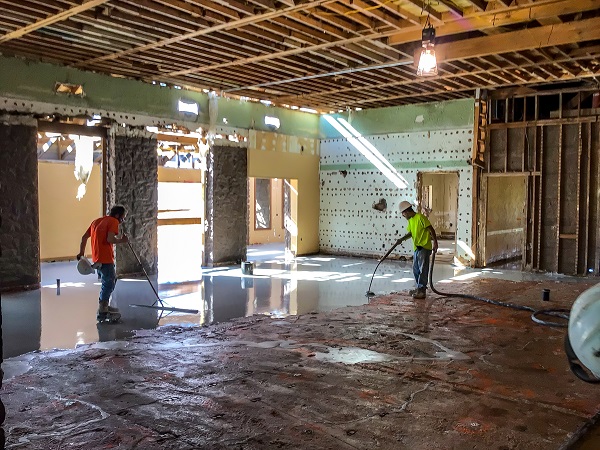
SOLUTION
Bill Ritchie and John Lowry of Gypsum Floors of AR/OK, Inc. were called to see if they could help. After a review of the structure, they recommended AccuLevel G-40. “I’ve poured it as thin as half an inch to as much as 2 inches” said Ritchie. “We have used it for several jobs and we always get excellent results.”
With the seasoned crew from Gypsum Floors of AR/OK onsite, the project took less than a day to complete. Working around the obvious challenges of the sublfloor, the end result was a remodel and the new addition now have a smooth flat surface that is as hard as a rock.
“The client was very happy” Ritchie said, “they got a floor better than what they hoped for.”
To view the case study – click here
Plenty of reason for optimism, industry stakeholders say
Aggregate demand has not been a problem of late for the industry, and expectations are high for healthy demand in 2022.
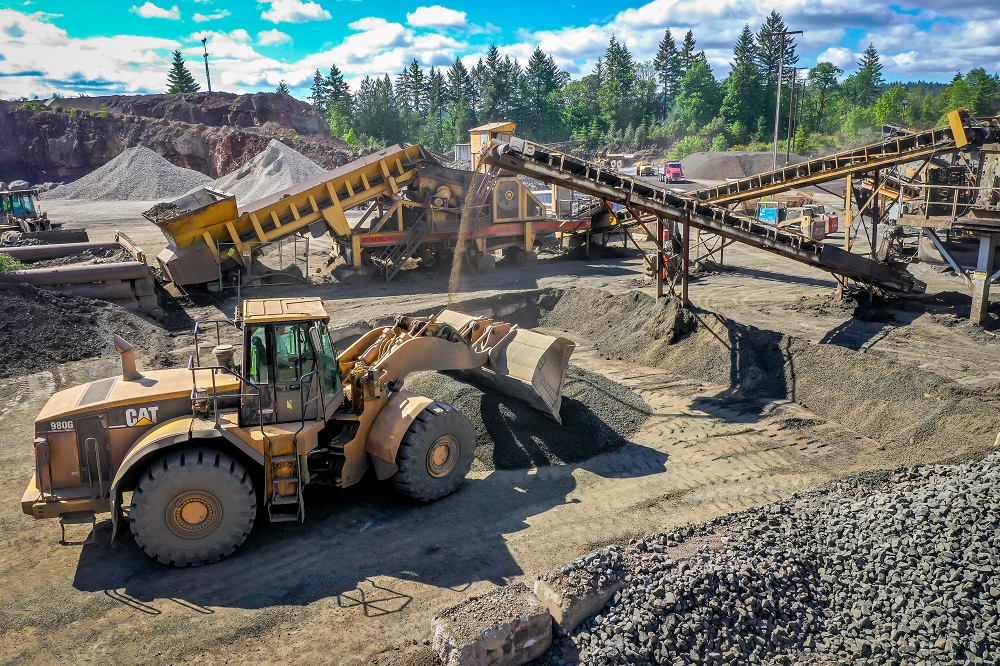
Optimistic.
That’s the word aggregate industry stakeholders use to describe their outlooks for 2022. But while the year promises no shortage of projects, the industry finds itself playing a supply-and-demand game: keeping up with the increased aggregate demand while navigating shortages and delays in the supply chain.
Boosted demand
Producers, equipment manufacturers and dealers tend to agree demand is up across the board. This is due, in part, to the Infrastructure Investment & Jobs Act (IIJA), which passed with bipartisan support in November.
Karen Hubacz, president and CEO of Massachusetts-based Bond Construction Corp., says the infrastructure bill’s components – namely industry exemptions, the ROCKS Act and enhanced permit streamlining – provide producers a much-needed confidence boost.
“It’s vitally important,” Hubacz says. “It’s really like an insurance policy for us in that we feel much more confident to put money into ourselves, specifically to maybe do plant improvements – things that cost a lot of money – because we know we’re going to invest this money in ourselves. But it’ll pay for itself sooner than later based on what we anticipate happening.”
IIJA’s passage was an added 2022 bonus for Unified Screening & Crushing, but the company was already planning for increased demand without it.
“There’s a lot of building, a lot of construction projects going on,” says Andrew Lentsch, COO of Unified. “So even without the infrastructure bill, I think there was still going to be an increase in demand. But, hopefully, that drives it even more.”
Similarly, The McLean Co., an Ohio equipment dealer, expects 2022 growth. Chris Reiser, the company’s crushing and screening specialist, describes his outlook as “cautiously optimistic” because of IIJA funds rolling out this year and his customers’ projections.
“You can forecast all you want on your own,” Reiser says. “You can say: ‘OK, we had 10 percent growth last year, let’s shoot for 15 percent this year.’ But at the end of the day, you’re only going to supply what’s needed. So if everybody you would otherwise sell to is growing, that’s a pretty good outlook for yourself as a business.”

Still, each year presents challenges. While increased demand and additional funding bodes well for industry stakeholders, supply shortages and delays aren’t going away anytime soon.
As of January 2022, Hubacz, Lentsch and Reiser each saw varying lead times for equipment, supplies and parts.
“Some are days,” Hubacz says. “Some are weeks. Some are months and months. Or, you get the ‘sorry, we just don’t know.’”
Hubacz adds that not knowing when parts will arrive can impact when projects get done.
“Even now, we can barely keep up with demand,” Hubacz says. “And then there’s a breakdown. We find out with the breakdown all we need is a simple sensor to fix the issue. You call your dealer [and] your dealer can’t tell you where one even is or when we will get it to you. So it is a giant problem.”
The McLean Co. supplies equipment coming from overseas. While its manufacturers have done a good job of getting equipment over as quickly as possible, Reiser says equipment sometimes gets stuck at backed-up shipping ports. It’s an issue that’s outside of a dealer’s or manufacturer’s control.
“So much of it depends on what these other countries are doing and what our port looks like,” Reiser says. “You could have a machine that you ordered six, eight months ago that’s finally coming in, but it might sit at [the] port for two to four weeks.”
Companies are also cautiously watching rising costs as 2022 unfolds. For Bond Construction, fuel prices are a factor to follow closely this year.
“The cost of doing business is on the rise,” Hubacz says. “This is mainly due to the elevated energy costs associated with gasoline and diesel. Everything from our aggregate production to our equipment needs are transported via trucks, plus all the different oil-based products we utilize every day. We’re all going to need to look at our bottom lines and make adjustments as needed.”
Unified Screening & Crushing, meanwhile, is hoping to see steel prices begin to level out at some point this year.
“Hopefully, the costs stabilize in the next 12 months,” Lentsch says. “There’s been quite a bit of increases over the last year to year and a half.”
Proving resilient
The concerns Hubacz, Lentsch and Reiser share are, of course, not new. These three and other industry leaders have been navigating the muddled supply chain and rising costs for the better part of the last two years.
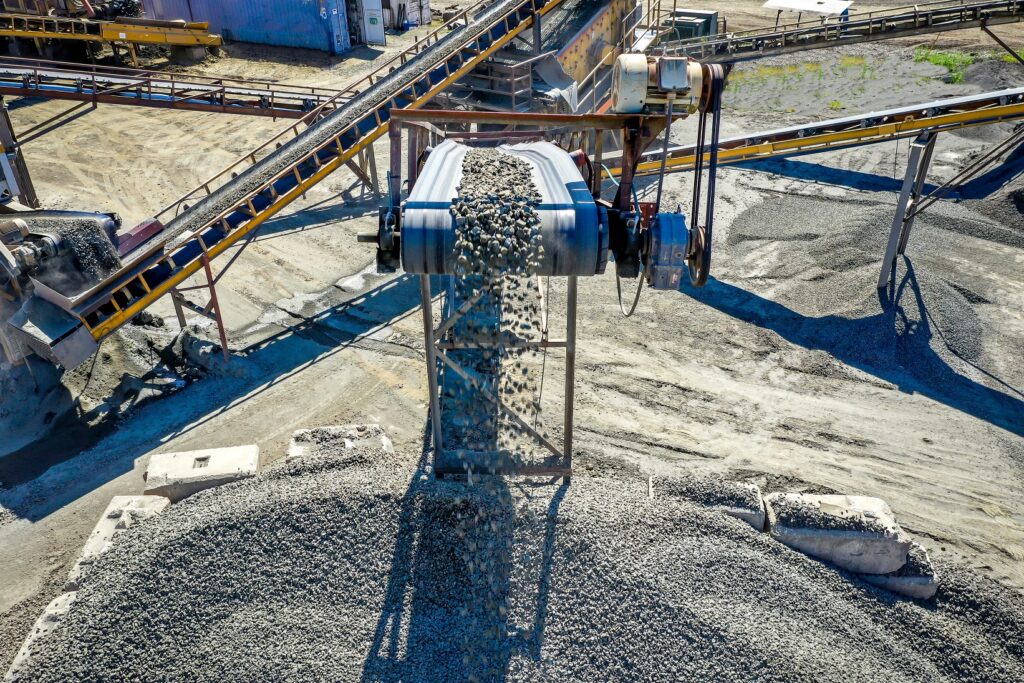
Most industry leaders at least agree 2020 and 2021 were, all things considered, better years than expected for the aggregate industry. In fact, Reiser says he’s already seeing minor signs of improvement with supply delays versus 2021.
“I don’t think it’s anything really different than it has been, at least last year, as far as delays go,” he says. “I don’t think anything’s more delayed. If anything, we’re probably less delayed on our side of things.”
The year ahead is promising, Hubacz, Lentsch and Reiser say, with funds from the infrastructure bill, the return of large trade shows and an increased number of projects. And there’s no doubt among stakeholders that the industry is primed for another year of success.
“The demand for aggregates is up,” Hubacz says. “Pricing for aggregates is holding steady and even improving. These two factors together will give producers a solid foundation to invest in their companies, which will be great for the whole industry.”
To view the original article – click here
How Climate Affects Concrete – Hot Weather, Cold Weather, and Wind
Know what your concrete will likely do when the weather starts to get too hot, too cold, and/or too windy.
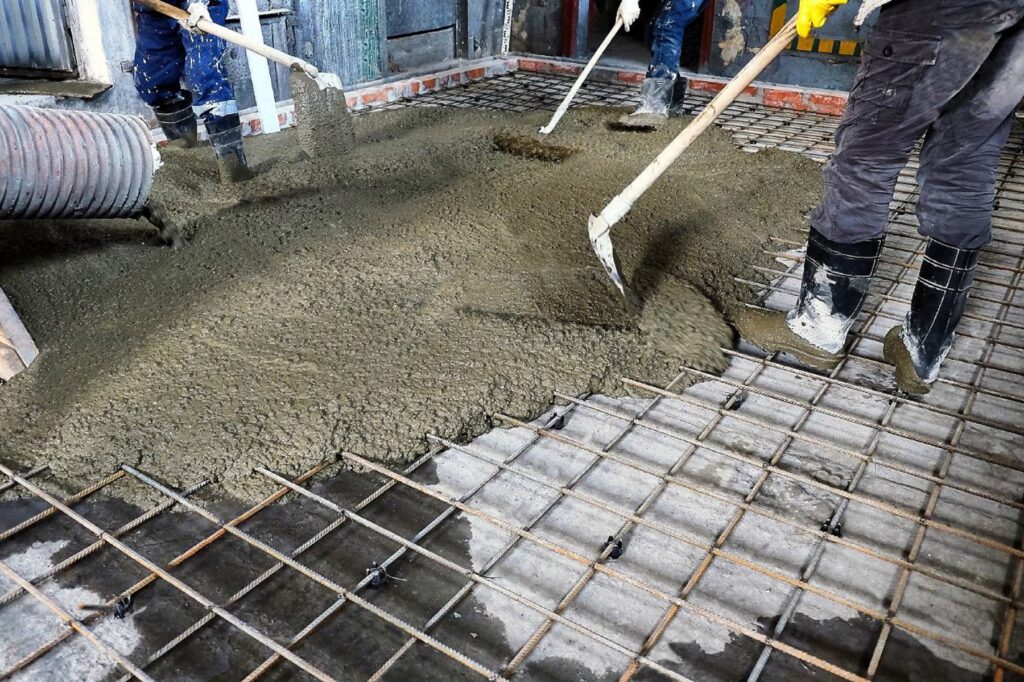
While working with concrete may come as second nature to many contractors, it is one of the trickiest substances to work with due to how quickly it can change when exposed to different temperatures, humidity, and wind rates. Ideal conditions for concrete are few and far between.
According to the ACI, concrete may be affected by, “…one or a combination of the following conditions that tends to impair the quality of freshly mixed or hardened concrete by accelerating the rate of moisture loss and rate of cement hydration, or otherwise causing detrimental results: high ambient temperature; high concrete temperature; low relative humidity; and high wind speed.” Under fair weather conditions, concrete can take anywhere from 8 to 48 hours to set properly. While concrete can reach its full strength in as little time as a week, it also takes nearly a month for it to cure properly.
However, anyone who has worked in construction before knows that weather conditions are seldom ideal.
While working with concrete may come as second nature to many contractors, it is one of the trickiest substances to work with due to how quickly it can change when exposed to different temperatures, humidity, and wind rates. The American Concrete Institute’s (ACI) technical publications are an excellent resource that provide insights regarding the plethora of effects of environmental factors on concrete. The ACI covers a variety of subtopics, ranging from extreme temperatures, humidity levels, wind velocity, natural disasters, saltwater, and freshwater’s effects on concrete in order to give contractors and concrete industry professionals accurate and up-to-date information.
Heat
The ACI’s (305.1 – 14 Hot Weather Concreting) specifications for setting and mixing concrete in hot weather suggests contractors should try to limit the maximum concrete temperature to 95º F. Contractors should ideally aim to work with, or pour, concrete when it is anywhere from 50-60º F. Under fair weather conditions, concrete can take anywhere from 8 to 48 hours to set properly. While concrete can reach its full strength in as little time as a week, it also takes nearly a month for it to cure properly.
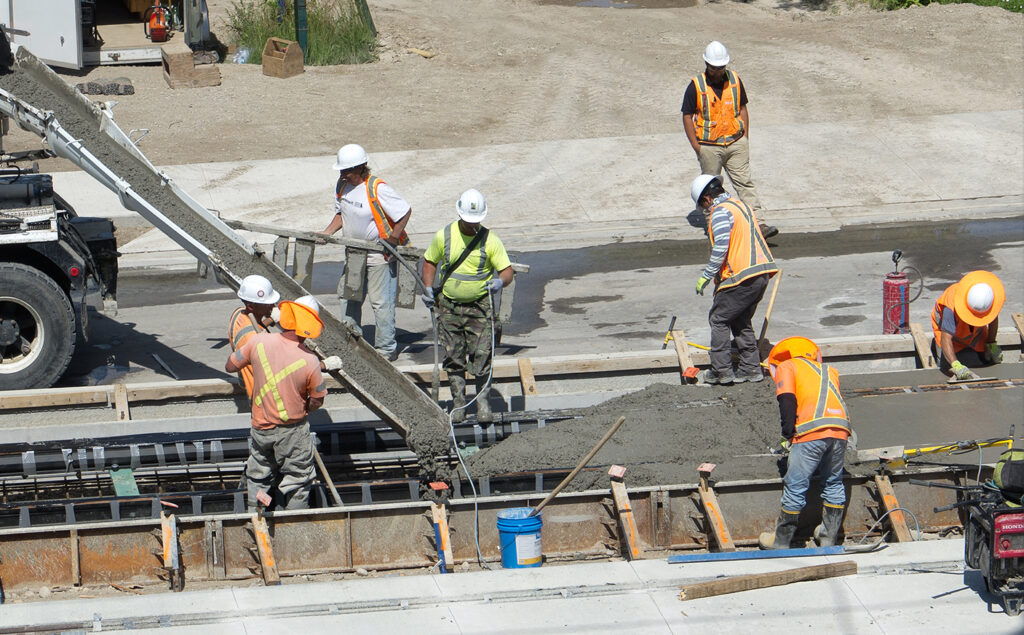
However, anyone who has worked in construction before knows that weather conditions are seldom ideal, which is why contractors must have a firm understanding of the effects of hot weather on concrete structures and how to use weather to their advantage.
For example, concrete is known to set quicker in hot weather when compared to cold weather. This is because moisture found in freshly poured concrete evaporates at a quicker rate in hot weather and subsequently allows for a faster setting time.
Due to the rapid evaporation of moisture, concrete that is poured during warm weather conditions is also more likely to experience cracks. Concrete will also be prone to more cracks if it is poured in a location where the weather cools down quickly during the night. Because of these effects, concrete that is poured and cured in 75º F weather will likely outperform concrete that is poured and cured in 100º F weather. Simply put, timing and background knowledge are absolutely crucial when it comes to working with concrete in warm weather.
Cold
Cold weather, according to the ACI 306 – “Guide to Cold Weather Concreting”, is defined as three continuous days of low temperatures, specifically below 40º F. Additionally, the ACI also considers air temperatures below 50º F for more than 12 hours as “cold weather.”
Unlike working with concrete in hot weather, where certain warm temperatures can be used to a contractor’s advantage, colder temperatures can be detrimental to newly poured concrete.
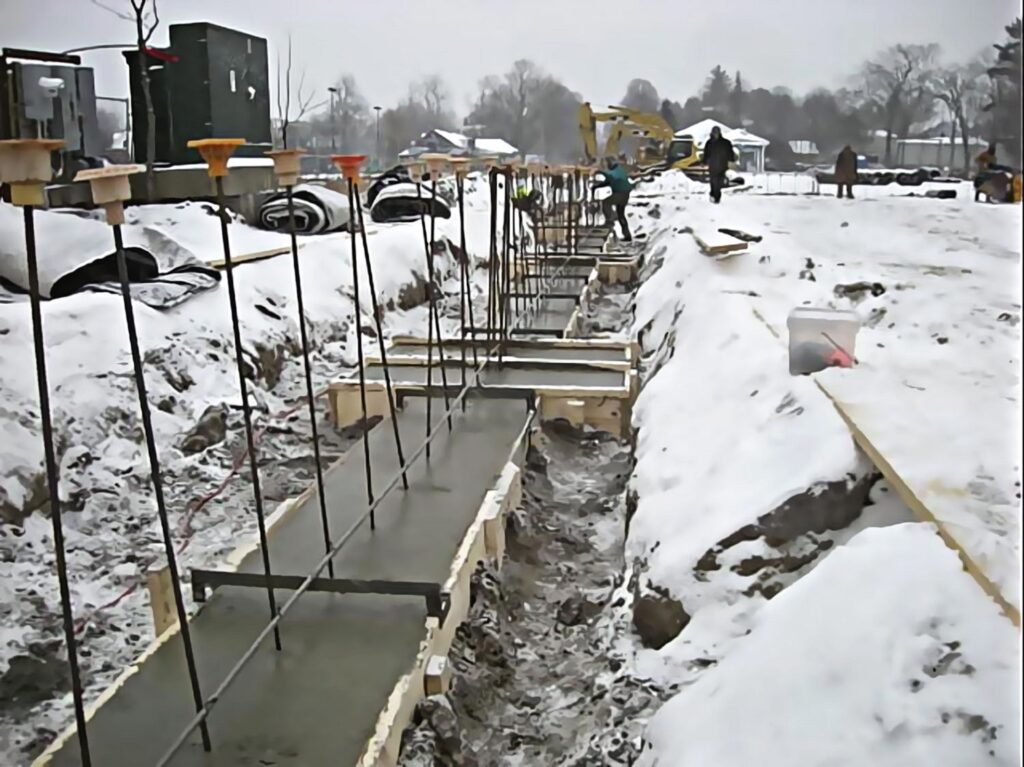
When a concrete powder is mixed with water, an immediate chemical reaction will occur which results in an internal crystallization of the concrete. These crystals make it possible for concrete to withstand additional pressure that may be caused by frozen water molecules within the concrete.
Crystals will continue to grow for an extended period of time, even in cold weather. However, if temperatures drop below 15º they will no longer grow and the concrete will not cure at its full compressive strength.
Under ideal weather conditions, concrete can attain a minimum compressive strength of roughly 500 lbs. per square inch in as little as 24 hours. This is much harder to achieve in colder climates, so contractors have learned industry tricks to “fool” the concrete into thinking it’s in warmer conditions so it will ultimately cure faster.
The ultimate contractor rule when working with concrete in cold weather: Never pour concrete directly onto frozen or thawed ground space. The frozen ground will actually settle as it thaws. Because of this, concrete that is poured in very cold temperatures could also be susceptible to cracking, similar to working with concrete in warmer climates.
Wind
The ACI also states that wind velocity can affect freshly poured concrete by allowing too much water or moisture to evaporate from the concrete’s surface at a fast rate. In fact, the ACI technically classifies high wind velocity under hot weather due to the similar excessive loss of moisture concrete can experience when poured in warmer temperatures.
When concrete is poured during extremely windy weather, the rapid velocity of air will only contribute to excess moisture evaporating from the slab of concrete. Because of this, the abrasion resistance and curing condition of concrete will subsequently suffer.
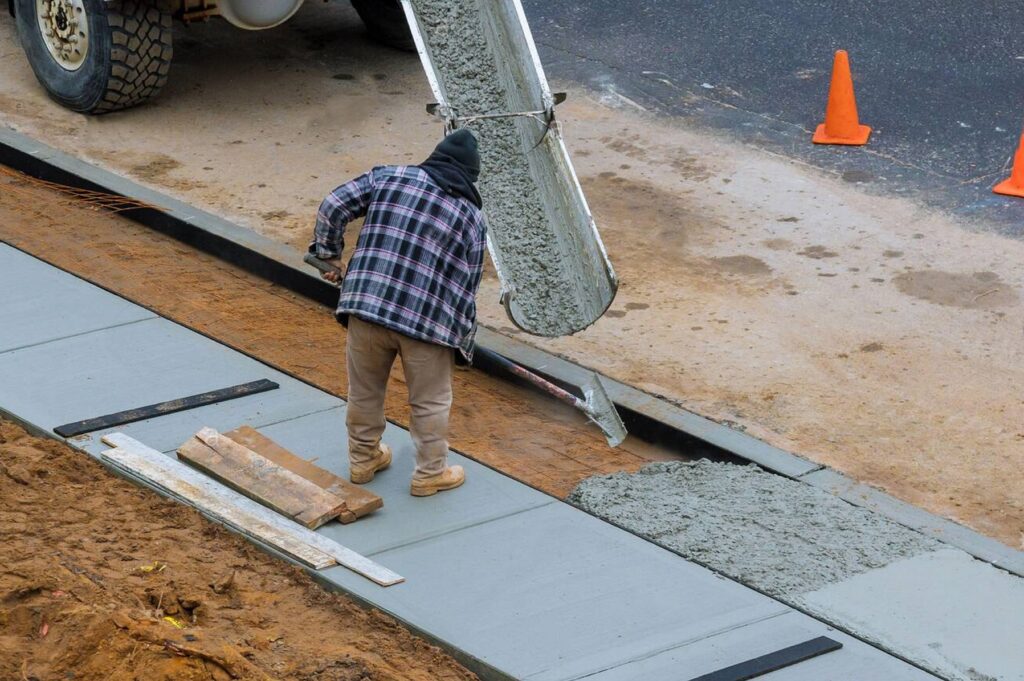
Colder winds can produce what’s called a “wind chill,” which can strip excess heat from concrete. Additionally, plastic shrinkage cracking can occur when the surface of concrete dries before it has fully cured. To combat wind chill, it isn’t uncommon for contractors to turn to heaters to aid the curing process. Contractors can also use sealers to protect concrete from climates below 50º F.
Concrete is a delicate material. Unbeknownst to many people, it is not only affected by extreme temperatures, but also by humidity levels, as well as the velocity and intensity of the wind. Working with concrete demands skill and patience. It requires both the expertise of those working with concrete, as well as the cooperation of environmental factors in order to produce a smooth, strong, properly cured structure.
To view the original article – click here
Surging Multifamily Housing Starts Beat Forecasts
Demand for apartments near major employment centers has strengthened, reducing vacancy rates and driving rents higher.
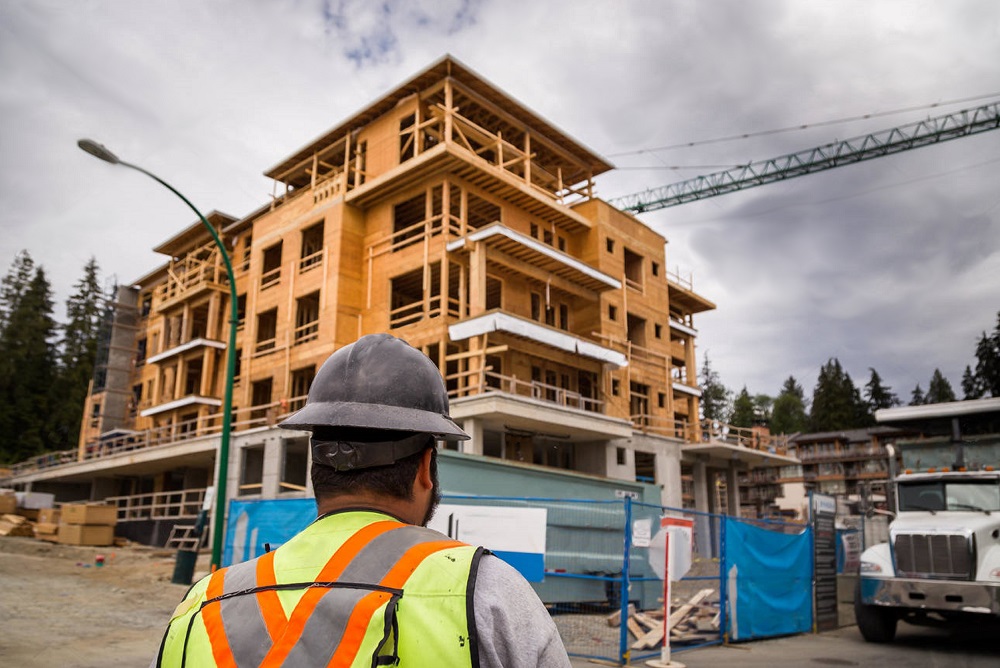
Multifamily starts leaped 20.6% to a 539,000-unit annual rate. Demand for apartments has been surprisingly strong and rents have risen, giving developers confidence to move projects forward.
Single-family U.S. housing starts fell 2.8% in August, but the surging multifamily construction raised overall starts to beat expectations, rising 3.9%. Building permits jumped 6.0%. Total starts hit a 1.62-million-unit annualized rate after revisions raised the July totals, according to data from the Department of Commerce on Tuesday. The median estimate in a Bloomberg survey forecast a 1.55 million pace.
The drop in single-family starts has more to do with supply and labor shortages than weakening demand. “Builders are increasingly having to limit sales, as they are uncertain when they will be able to complete homes due to ongoing shortages of essential building materials,” says Mark Vitner, senior economist with Wells Fargo Securities.
The impact of supply shortages shows up in the rising number of single-family homes that have been permitted but not started, up 1.4% in August and 50% over the past year. Shortages are widespread. Similar to what is happening in the auto sector, a single part such as panel box or wedge anchors, can hold up construction.
Details in the Digits
Multifamily starts leaped 20.6% to a 539,000-unit annual rate. Demand for apartments has been surprisingly strong and rents have risen, giving developers confidence to move projects forward.
“The apartment market is seeing somewhat of a reversal of the pandemic exodus,” says Vitner. “Demand for apartments near major employment centers has strengthened, reducing vacancy rates and driving rents higher. Demand also remains strong in the suburbs, with many potential renters opting to renew their lease and wait for housing inventories to normalize.”
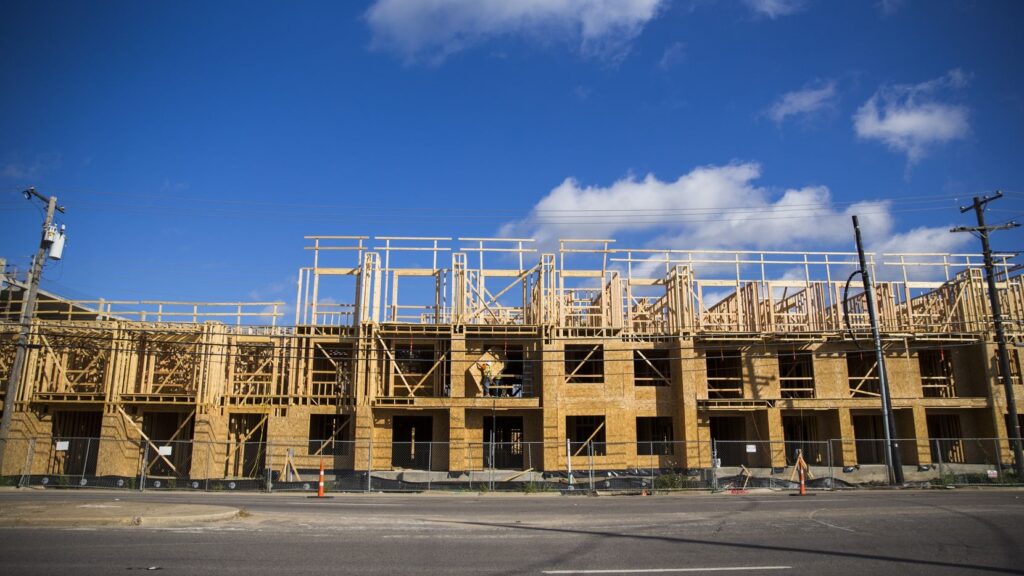
“The apartment market is seeing somewhat of a reversal of the pandemic exodus,” says Vitner. “Demand for apartments near major employment centers has strengthened, reducing vacancy rates and driving rents higher. Demand also remains strong in the suburbs, with many potential renters opting to renew their lease and wait for housing inventories to normalize.”
August’s 2.8% slide in single-family construction follows a 4.7% drop in July, but single-family construction remains at a robust 1.076-million-unit pace. Spot-market prices for lumber have plummeted, but those lower prices have not yet made their way to home builders.
Other essential building materials remain in short supply, including windows, cabinets, electric breaker boxes and wedge anchors. Builders are restricting sales due to the inability to let buyers know when homes will be completed.
Builder Confidence Rises in September
The September Housing Market Index (HMI) from the National Association of Home Builders and Wells Fargo points to where the single-family market is headed. The HMI rose one point in September to 76. While the index remains at a high level, it has been cooling since hitting an all-time high of 90 in November. The latest survey shows concerns about lumber prices have eased considerably, but builders are still dealing with widespread materials shortages, which is lengthening the time it takes to complete a home.
“The most encouraging aspect of the September HMI is the slight improvement in underlying demand,” says Vitner. “The present sales index rose one point to 82, following four months of decline.”
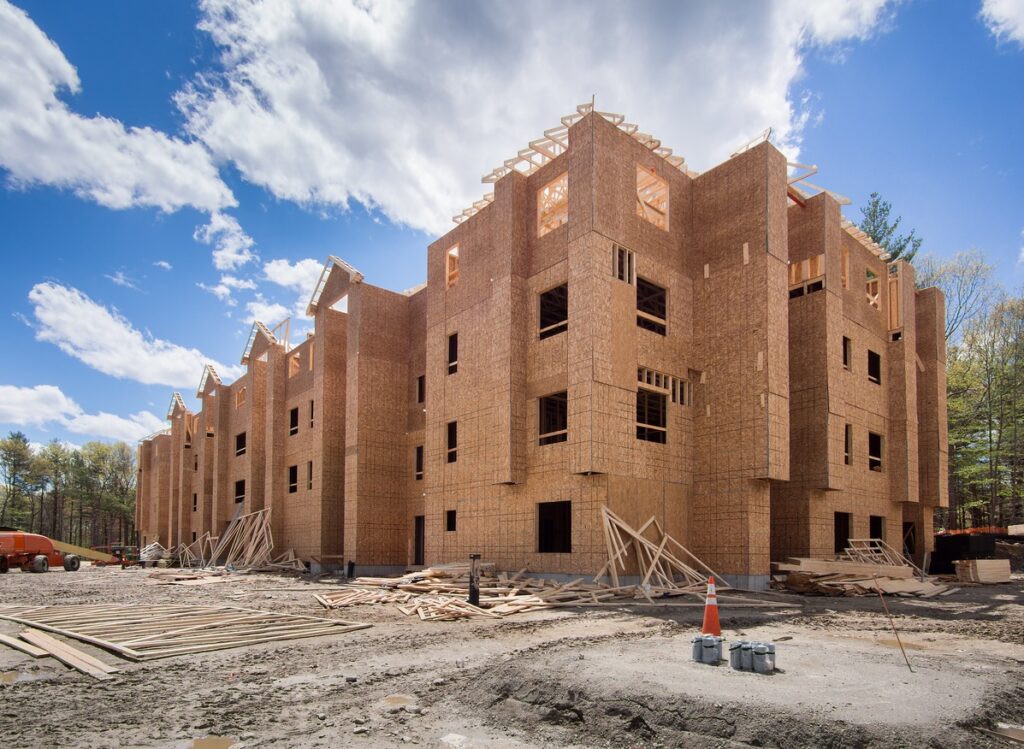
“The most encouraging aspect of the September HMI is the slight improvement in underlying demand,” says Vitner. “The present sales index rose one point to 82, following four months of decline.”
Prospective buyer traffic improved, although it remains well below levels seen earlier this year. Demand for homes remains strongest in the South and West, particularly the Mountain West. New home sales are increasingly being driven by the affordability migration from the West Coast and Northeast to more affordable markets in the Rocky Mountains, Southwest and Southeast. The influx of buyers from higher-priced housing markets has skewed new home sales more toward the upper-end of the price spectrum. Builders have focused their attention at this end of the market as well, contributing to the dearth of more affordable homes currently on the market.
To view the original article – click here
Concrete and cement industries brace for demand boom
$1 trillion infrastructure plan looks to create increased demand.
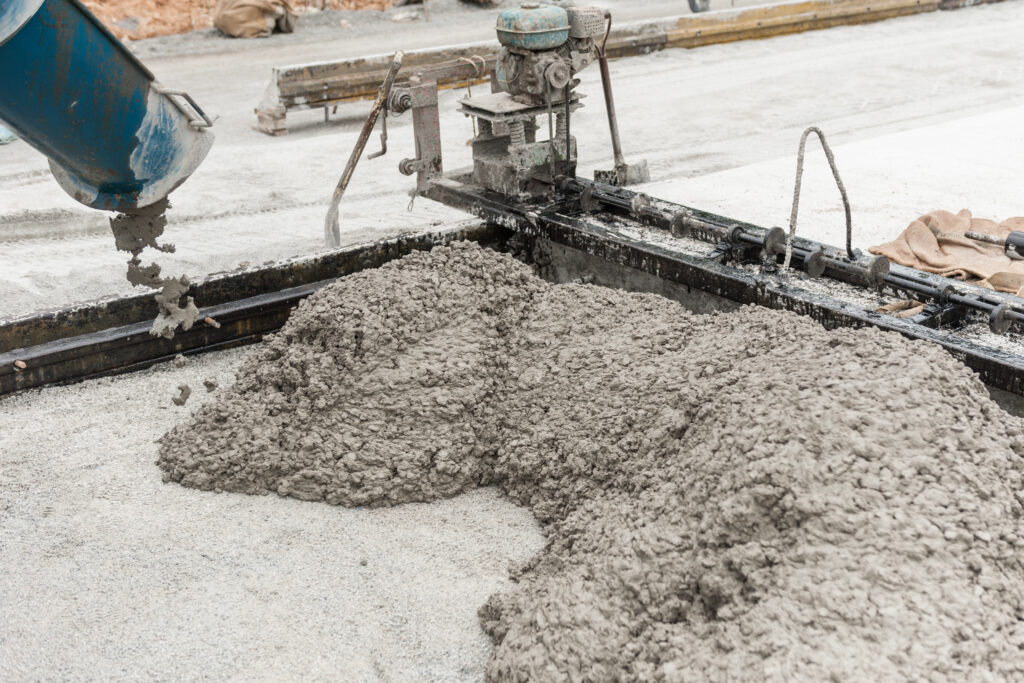
Concrete is the foundation of just about everything. It’s used to construct buildings, highways, bridges, roads and more.
During the Covid-19 pandemic, concrete fell victim to the same phenomena impacting other essential materials and goods: snarled supply chains and labor shortages. And demand for concrete — and its essential ingredient, cement — appears to have only increased, after the Senate passed the $1 trillion infrastructure package to upgrade America’s roads, bridges and tunnels.
“In the short-term, we continue to have the supply chain difficulties, particularly in certain markets, and so prices are rising,” Anirban Basu, chief economist for the national construction industry trade association Associated Builders and Contractors, told CNBC. “So right now, apparently, supply is not rising up to meet demand.”
The industry also faces labor shortages of skilled workers and truck drivers. And the recent housing boom means more demand for concrete and cement, putting more pressure on the industry to increase capacity.
On top of all of this, there’s also a push to reduce the amount of carbon emissions that come from the industry. A study published by the National Academy of Sciences in 2019 estimates that global cement production accounts for 8% of global carbon emissions, making it the largest single industrial emitter of carbon dioxide.
Watch the video
to learn more about the cement-concrete supply chain and whether the U.S. industry can handle the coming demand from the new $1 trillion infrastructure spending plan.
Here is a link to a video that does a great job explaining the current and forecast demand:
To view the original article – click here
Multifamily construction remains strong
2021 multifamily housing outlook: Dallas, Miami, D.C., will lead apartment completions
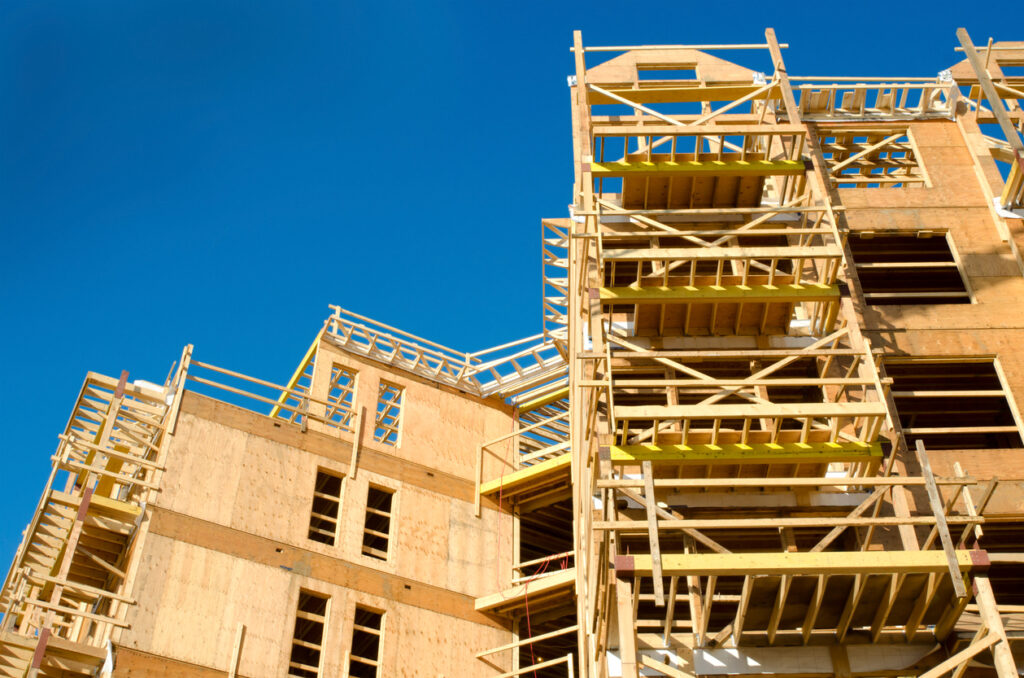
In its latest outlook report for the multifamily rental market, Yardi Matrix outlined several reasons for hope for a solid recovery for the multifamily housing sector in 2021, especially during the second half of the year.
While multifamily owners, developers, and property managers collectively braced for severe drops in rent growth, construction starts, project completions, and availability of capital amid the COVID-19 pandemic, the drastic declines never materialized.
Rent growth did take a step back in select markets, especially in “high-cost gateway” metros like San Jose (-13.7%) and San Francisco (-9.4%), as renters continued to leave pricey urban neighborhoods for less-dense, cheaper suburban areas.
But on the flip side, “many tertiary and tech hub markets have benefited from migration out of the gateways,” wrote the authors of the Yardi Matrix report. Secondary and tech markets like the Inland Empire, Sacramento, Tampa, and Las Vegas all saw solid rent growth in 2020.
Multifamily construction pipeline for 2021
Other than the temporary shutdowns of work sites during the pandemic, construction work on multifamily housing developments continued to hum along through 2020 and into 2021. In all, 285,000 multifamily units were delivered throughout U.S. markets in 2020, down about 7% from 2019, but not nearly as severe a drop as many had predicte
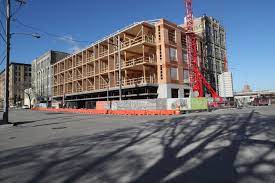
According to Yardi Matrix, the multifamily sector has a “robust pipeline” of new projects, with some 765,000 units in some stage of construction as of early 2021.
This “should keep deliveries above that 300,000 mark for the next few years.” The firm projects 327,718 units will be delivered in 2021.
Here are the top 25 multifamily markets for 2021 (total number of construction completions, % growth in completions YOY):
- Dallas: 22,909 completions (+12.1% YOY)
- Miami: 16,262 (+66.3%)
- Washington, D.C.: 14,541 (+50.5%)
- Houston: 11,500 (-3.1%)
- Los Angeles: 11,296 (+16.5%)
- Atlanta: 10,939 (+9.7%)
- Austin: 10,301 (-10.0%)
- Seattle: 9,816 (+29.9%)
- Phoenix: 9,334 (+13.6%)
- Denver: 8,653 (-29.7%)
- Boston: 8,449 (+20.8%)
- Chicago: 7,797 (+0.8%)
- New York City: 7,335 (+24.2%)
- San Francisco: 7,166 (+64.8%)
- Twin Cities: 6,760 (+4.9%)
- Charlotte: 6,692 (+55.3%)
- Orlando: 6,662 (+21.5%)
- Philadelphia: 6,071 (+27.7%)
- Nashville: 5,457 (+41.1%)
- Tampa–St. Petersburg: 5,103 (+20.1%)
- San Antonio: 4,960 (-6.5%)
- New Jersey–Northern: 4,955 (+29.9%)
- Salt Lake City: 4,633 (-0.6%)
- Louisville: 4,484 (+215.6%)
- White Plains: 4,464 (+199.6%)
To view the original article – click here
Gypsum an Important Source of Sulfur
Sulfur important in plant growth.
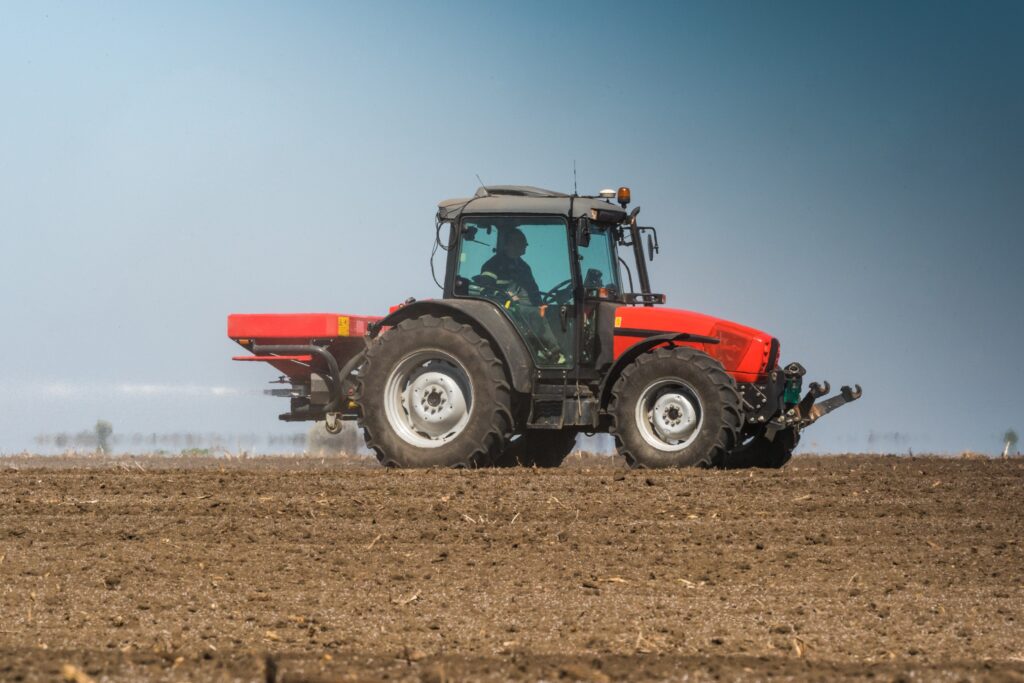
Long taken for granted as supplied by the soil and atmosphere, sulfur is slowly rising as a yield-limiting nutrient in crops across the US.
Ken Ihlenfeld is certainly finding this to be true. The West Bend, WI, producer farms 2,500 acres including 400 acres of alfalfa used for his 400-head dairy operation. When his standard soil test couldn’t explain the yellowing and unevenness in his alfalfa fields he dug deeper including tissue testing for secondary macronutrients and micronutrients. “We discovered sulfur levels were really low,” he says.
He spread one ton of gypsum — a source of sulfate sulfur and calcium — per acre after the first cutting on 150 acres of alfalfa and Ihlenfeld noticed a significant difference.
“There was a 6-inch height difference, the plants were greener and the crop was lush,” he says. “The treated acres yielded 0.6 tons more than the untreated acres on a dry matter basis.”
The success prompted him to apply gypsum on the rest of his alfalfa acres and to some corn and soybean ground.
“Already this spring our hay fields are greener and more even in color than our neighbors that haven’t applied gypsum and the check strips we left are very noticeable,” he says.
After hearing repeated farmer accounts of sulfur improving corn yields, Fabian Fernandez, researcher and assistant professor of soil fertility and plant nutrition at University of Illinois, decided to test response himself. His three years of research farm and on-farm trials seem to confirm the reports.
“We have seen an increase in the frequency and intensity of crop response to sulfur application compared to Illinois trials conducted in the late 1970s which showed little to no response,” he reports. “The responses are very variable, but we are identifying conditions where sulfur applications will be beneficial for farmers.”
Results from a 2006 Iowa State University study on corn yield response to sulfur application showed an average 38-bushel yield response to sulfur application for six sites across northeast Iowa. These sites were specifically chosen for their likelihood of being sulfur deficient.
In small research farm plots not specifically chosen for deficiency, Fernandez found a more moderate average 5-bushel corn yield response to sulfur applications over three years. One of his Illinois on-farm plots, though, yielded surprising results.
“It produced a one-year, 51-bushel corn increase over the check with an application of sulfur,” Fernandez says. “That’s not a normal response by a long shot, but it goes to show that if sulfur is truly deficient it can severely limit yields.”
Less sulfur in rain
Sulfur deposits on farm fields have decreased over the years, in part as a result of emission-reducing technologies used at coal-fired power plants. There is less sulfur in the atmosphere and in rain that hits farm fields.
There is no simple test for determining sulfur deficiency on individual farms, says Warren Dick, a researcher and former professor in Environmental and Natural Resources at The Ohio State University. Researchers have found, however, that certain factors can increase the likelihood of seeing a response to sulfur.
Soil type, cropping history and the crop planted can help determine on which acres farmers should try using sulfur. Soils with low organic matter are a good place to start as mineralization from organic materials is one of the leading sources of soil sulfur.
“Soils with low organic matter, such as coarse texture (sandy) soils or eroded soils likely found on sloping hills, are more likely to be low in sulfur and respond to sulfur applications,” Fernandez says.
Sulfur is an essential ingredient for creating proteins, so high-protein crops (alfalfa, canola, soybean, corn silage) require more sulfur than low-protein producing crops. A lack of sulfur can impact nitrogen utilization and yield.
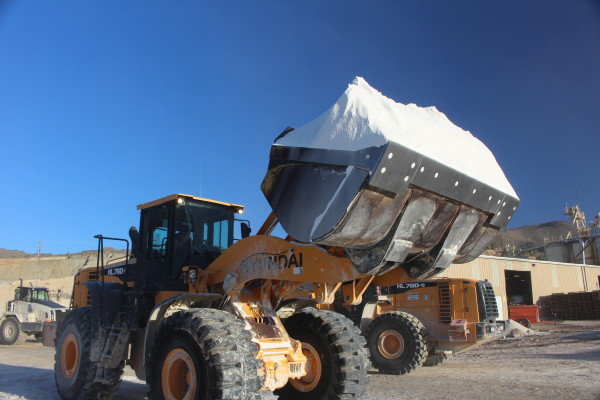
There are several sulfur sources producers can use to meet crop demand including elemental sulfur one primary source is anhydrite and dihydrate gypsum.
Estimates vary, but roughly one pound of sulfur is needed to be applied to balance up to 16 pounds of applied nitrogen for a corn plant to produce proteins and grow. If there’s adequate nitrogen but deficient sulfur the plant won’t grow to its potential until it has the sulfur to balance that nitrogen. Deficiencies are particularly critical in early growth corn because that’s when yield potential is set. If the upper soil profile, where seedlings are growing, is deficient of sulfur there will be less yield potential.
Sulfur can be recycled back into the soil system through crop residue, Dick says, but in crops such as corn and alfalfa much of the protein — and sulfur — is removed with harvest.
“A 250-bushel corn crop removes quite a bit of sulfur every year without replacing it,” Dick says. “The same is true of hay fields. A lot of nutrients are removed when hay is cut and taken from the field, making alfalfa fields and mixed hay pastures good places to try sulfur applications.”
Sulfur Sources
There are several sulfur sources producers can use to meet crop demand including elemental sulfur one primary source is gypsum.
“Elemental sulfur is used, but it is very acid forming so it isn’t ideal for every situation,” Dick says.
At 16 percent sulfur by volume, gypsum is a budget-friendly option. The cost of a pound of sulfur in gypsum is significantly lower than sulfur in other forms. It also provides sulfur in a plant-available form and moves sulfur through the soil profile so it’s where it needs to be in the form it needs to be in for plants to use it. Gypsum provides the added benefit of 17-20 percent calcium and is often used in potato production and other calcium-loving specialty crops.
Extensive studies have shown all of the various gypsum sources are safe for land application, says Dick.
For Center Point, IN, producer Brad Brown, gypsum provides the double benefit of building soil structure and replenishing sulfur.
“We didn’t know about sulfur when we first started using gypsum in 1986 to loosen our soil for better drainage and rooting,” Brown says. “Getting sulfur with our gypsum was a win-win, it really helps our corn and it’s in the cheapest form we can get. Our yields are more even from acre to acre and year to year. The sulfur seems to excite the corn for good early season growth.”
Brown applies gypsum every other year. Initially he applied one ton per acre but has dropped to 1,400 pounds every other year applied in the fall ahead of corn.
“As the soil structure builds we’re able to cut back on the rate but we will keep applying it to maintain the sulfur supply for our corn. We shoot for 200-plus bushels per acre,” specifies Brown.
Wisconsin producer Ihlenfeld agrees gypsum is becoming a valued tool in his cropping operation. “We were attributing sulfur deficiency symptoms to disease, but now that we know what it is we’re able to correct the situation and our yields improved after only one application,” Ihlenfeld says. “Gypsum is a win-win for us because it boost yields by correcting the sulfur deficiency and the calcium helps loosen up our compacted soils.
To view the original article – click here
Concrete Technology 2021
Greener Every Year and 35% Stronger
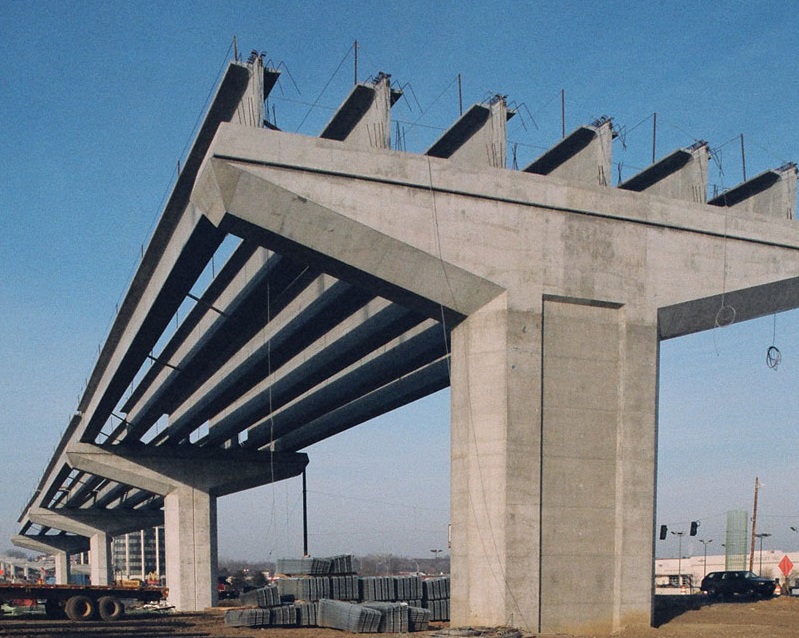
In our era of “carbon neutral” construction materials and green energy trends, the term “green concrete” has evolved to describe an environmentally friendly construction material.
The term “green concrete”, not so many decades ago, used to describe the condition of freshly poured ready mix concrete in construction projects or precast concrete products that required more curing time to achieve its full average 3,000 psi strength. The term “green” as applied to concrete was all about quality control.
Now, in our era of “carbon neutral” construction materials and green energy trends, the term “green concrete” has evolved to describe an environmentally friendly construction material.
Recycling and Concrete
Concrete is the most durable construction material in the world, and like the concrete used by the Egyptians to build the pyramids, an incredible 5,000-year lifespan for concrete structures isn’t unusual. But with the ever-changing demands of human civilization, the demolition of old obsolete concrete buildings and structures is inevitable.
But what can be done to dispose of the concrete rubble, a construction material with such incredible resilience to the elements that it’s not going to break down naturally in landfills any time soon? The answer is simple. Use the old concrete to make the aggregates for new concrete.
Fortunately, the crushing characteristics of hardened concrete are nearly equivalent to natural rock. That means that the original quality of the recycled material isn’t a factor, except for the poorest quality original concrete. As an aggregate for new concrete, the recycled rubble actually has advantages. Since all the original aggregate components are there as well as the existing hydrated cement paste, recycled concrete aggregates add more to enhance binding and strength characteristics than virgin crushed rock and sand alone.
With over 70% of the world’s population living in structures that contain concrete, the most natural disaster-resistant building material available, only one other substance on the planet is consumed more by human society. That substance is water.
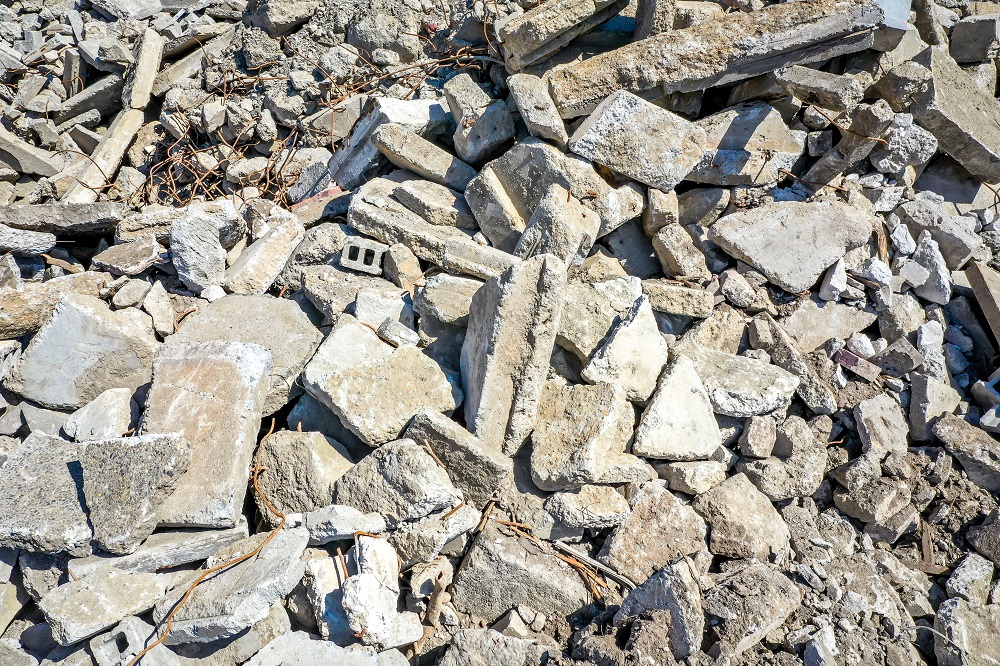
Under increasing environmental pressures, diverting concrete waste from landfills is another top priority for the industry.
New Research
In the US more than 55,000 miles of highway are paved with concrete. With such widespread use, scientists are constantly looking for innovative ways to make concrete even more resilient by increasing strength and heat resistance with new additives and aggregate enhancements.
Now scientists from Australia’s RMIT University may have come up with a win/win solution in the search for better concrete construction materials with a new recycled concrete aggregate that’s a superior choice for paving those 55,000 miles of highway.
In his informative January 2021 article at New Atlas Nick Lavars reports on how RMIT research has led to the addition of recycled rubber tires and concrete demolition rubble in the traditional time-proven concrete formula of portland cement, sand, crushed rock, and water. First developed for paving, the RMIT team is now moving on to develop the innovative recycled concrete formula for precast concrete products.
Arcosa Specialty Materials provides Gypsum Dihydrate and Gypsum Anhydrite to the largest cement manufactures in the nation. Our sister company, Arcosa Aggregates, has concrete recycling facilities.
To view the original article – click here